subname
FACTORY ACCPETANCE TEST (FAT)
Factory Acceptance Test (FAT) is a comprehensive testing conducted by suppliers in a factory environment before the equipment or system leaves the factory, aimed at verifying whether the equipment meets contract requirements, technical specifications, and user needs. FAT is a critical link in the project lifecycle, ensuring that equipment has high quality and reliability before delivery, and reducing the risks of on-site debugging and installation.
Factory Acceptance Test (FAT) is a comprehensive testing conducted by suppliers in a factory environment before the equipment or system leaves the factory, aimed at verifying whether the equipment meets contract requirements, technical specifications, and user needs. FAT is a critical link in the project lifecycle, ensuring that equipment has high quality and reliability before delivery, and reducing the risks of on-site debugging and installation.
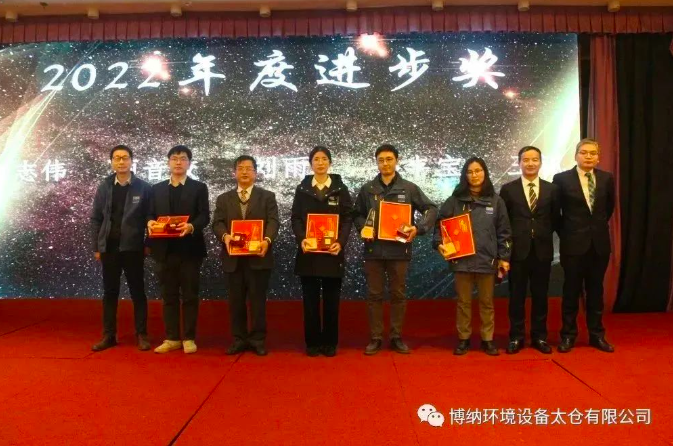
Factory Acceptance Test (FAT) is a comprehensive testing conducted by suppliers in a factory environment before the equipment or system leaves the factory, aimed at verifying whether the equipment meets contract requirements, technical specifications, and user needs. FAT is a critical link in the project lifecycle, ensuring that equipment has high quality and reliability before delivery, and reducing the risks of on-site debugging and installation.
The main purpose of FAT
Verify device functionality
Ensure that the equipment can operate normally under standard conditions, meet design requirements and user needs.
Identify potential issues
Identify and resolve hardware, software, or integration issues in advance in the factory environment to avoid delays during on-site debugging.
Confirm technical specifications
Verify whether the device performance, parameters, and interfaces comply with the contract and technical agreement.
Train users
Provide operation and maintenance training to end-users to ensure familiarity with equipment usage.
The core content of FAT
Hardware Testing
Appearance inspection: equipment integrity, labeling, connectors, etc.
Electrical testing: voltage, current, power, insulation, etc.
Mechanical testing: Moving parts, structural strength, durability, etc.
software test
Functional testing: Verify whether the software functions meet the requirements.
Performance testing: response time, throughput, stability, etc.
Compatibility testing: Interface compatibility with other systems or devices.
System Integration Test
Subsystem joint debugging: Verify the collaborative work between subsystems.
Interface testing: Ensure consistency in communication protocol and data format.
Safety testing
Protection functions: overload protection, emergency stop, safety interlock, etc.
Compliance: Complies with industry standards such as CE, UL, ISO, etc.
Documentation Review
Technical documents: operation manual, maintenance manual, schematic diagram, etc.
Test report: FAT test records, problem list, and solutions.